STOP ZALIHAMA! Kaizen™ knjiga, Masaaki Imai
Ispred Motomachi fabrike u sastavu kompanije Toyota čeka dug red kamiona punih auto-delova i komponenti za montažnu liniju. Novi kamion uđe u fabriku čim neki prethodni napusti fabrički krug. Nema skladišta za te delove. Tapacirana sedišta, na primer, stižu do proizvodne linije direktno iz kamiona.
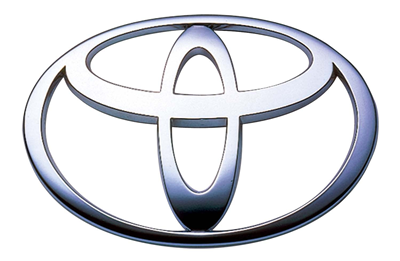
TPS (Toyota Production System) privlači veliku pažnju u Japanu i van njega zato što je Toyota među onim kompanijama koje su preživele naftnu krizu i očuvale visok nivo profitabilnosti. Obilje činjenica dokazuje uspeh fabrike. Toyota nema nikakvih dugovanja, zarađuje koliko i najveća japanska banka.
Toyota je 1966. godine prva primila cenjenu Japansku nagradu za kontrolu kvaliteta. Pročula se po izuzetnim sistemima kontrole kvaliteta. Samo je sedam kompanija do dana današnjeg primilo tu nagradu. Toyota je čuvena i zbog sistema radničkih predloga. Njen sistem proizvodnje, nazvan kamban, priznat je kao uspešniji od sistema naučnog upravljanja (Frederick Taylor) i sistema masovne proizvodnje na montažnim trakama (Henry Ford).
Začetnik TPS koncepta Taiichi Ohno tvrdi da se ovaj sistem rodio iz potrebe za razvojem sistema za proizvodnju malog broja različitih automobila. Taj pristup je suprotan zapadnjačkoj praksi proizvodnje velikog broja istovetnih vozila. Ohno se istovremeno usredsredio na eliminisanje svih vrsta gubitaka. Da bi to učinio, razvrstao je gubitke do kojih dolazi u procesu proizvodnje u sledećih 7 kategorija:
- hiperprodukcija
- gubici u čekanju
- gubici u transportu
- gubici u procesu (over-processing)
- gubici u zalihama
- gubici u pokretima, i
- gubici u defektnim proizvodima.
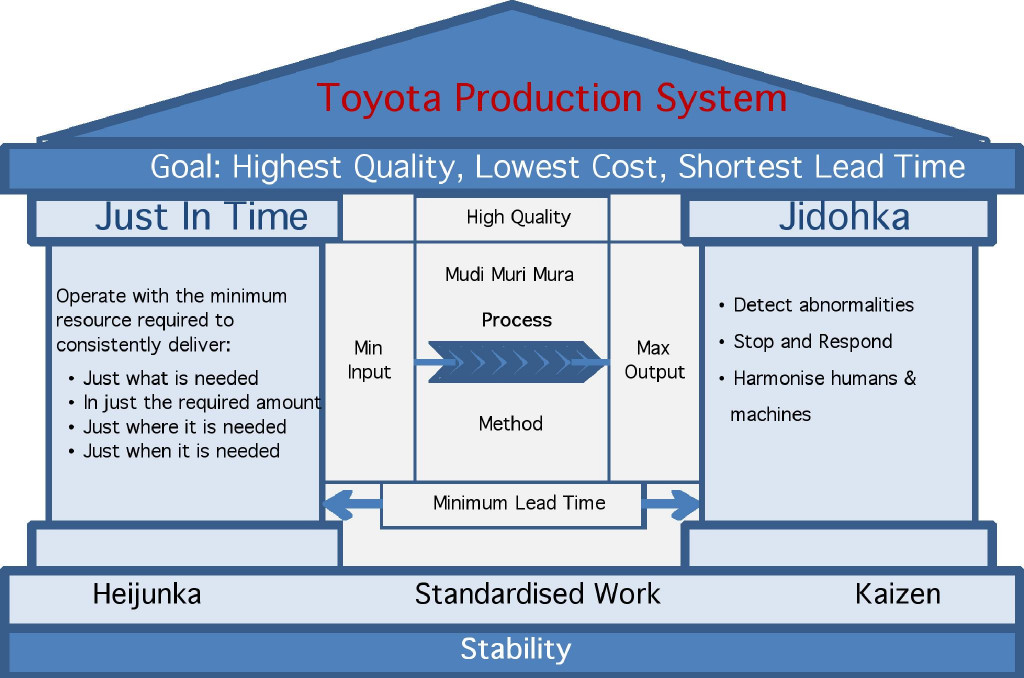
Ohno je osećao da je hiperprodukcija centralno zlo koje vodi do gubitaka u ostalim oblastima. On je, da bi eliminisao problem, smislio sistem proizvodnje zasnovan na dve najvažnije strukturalne osobine: (1) koncept just in time i (2) jidoka (automatizacija sa ljudskim dodirom).
Koncept just in time znači da se uvek isti broj potrebnih jedinica prinosi svakoj narednoj fazi proizvodnje u određeno vreme. Uvođenje ovog koncepta u praksu zahtevalo je izokretanje normalnog procesa razmišljanja. Jedinice bi se obično transportovale do sledeće proizvodne faze čim bi bile gotove. Ohno je preokrenuo ovaj redosled. Od svake faze se zahteva da se vrati do prethodne da bi tamo uzela potreban broj jedinica. Ovo je dovelo do znatnog pada u nivou zaliha.
Ohno je 1952. godine smislio kamban koncept. Iste godine je počeo probni rad u mašinskoj i montažnoj jedinici. Prošlo je 10 godina dok sistem nije u potpunosti usvojen u svim Toyota fabrikama. Kada je sistem bio utvrđen u kompaniji, Ohno je počeo da ga širi na podugovarače. U početku je pozivao podugovarače u obilazak fabrike. Slao je svoje inženjere na konsultacije sa podugovaračima. Isporuka jedinica koje stižu just in time za montažne operacije je rezultat zajedničkog napora kompanije Toyota i njenih podugovarača.
Kamban u prevodu znači „tabla ili poruka“. On igra ulogu komunikacionog alata u sistemu. Kamban se pričvrsti na svaku kutiju delova upućenu ka montažnoj liniji. Delovi se upućuju ka liniji u trenutku potrebe, pa kamban može biti vraćen kada se svi delovi iskoriste. Tada predstavlja dokaz o obavljenom poslu i porudžbinu za nove delove. Lepota ovog sistema jeste ta što kamban usklađuje priliv delova i komponenti montažnoj liniji, minimalizujući proces i omogućavajući, na primer, da blok motora donet u fabriku ujutru iste večeri jezdi drumovima u novom automobilu. Kamban sistem je alat u okviru TPS koncepta. On nije cilj sam po sebi.
Koncept just in time nudi sledeće prednosti: (1) skraćuje vreme trajanja procesa, (2) skraćuje vreme potrošeno na posao van procesa, (3) smanjuje zalihe, (4) poboljšava ravnotežu među različitim procesima i (5) razjašnjava probleme.
Osnovna strukturalna karakteristika TPS koncepta je jidoka. Jidoka je termin skovan za mašine načinjene tako da se automatski zaustave kad god dođe do nekog problema. Sve mašine u kompaniji Toyota imaju automatski mehanizam za zaustavljanje. Kada se u Toyota sistemu proizvede defektna jedinica, mašina staje, a sa njom i čitav sistem. Izvodi se osmišljeno prilagođavanje da bi se sprečilo ponavljanje iste greške, ne pristupa se ishitrenim rešenjima. Taiichi Ohno tvrdi da je to donelo revolucionaran proboj u konceptu proizvodnje. Radnik ne mora da stoji kraj mašine dok ona dobro radi, već samo kada se zaustavi. Jidoka omogućava jednom radniku da istovremeno opslužuje više mašina što izuzetno poboljšava njegovu produktivnost.
Pošto zaposleni istovremeno nadziru više različith mašina, sistem dovodi do znatnog proširenja radnikove odgovornosti i veština. Radnik, sa druge strane, mora biti voljan da usvoji niz novih znanja. Ovaj pristup omogućava i veliku prilagodljivost u prostornom rasporedu mašina i procesu proizvodnje. Isti koncept je proširen na ručni rad na montaži. Zaposleni je ovlašćen da zaustavi liniju kad god utvrdi da nešto nije u redu.
Zamka savremene automatizacije je hiperprodukcija delova bez obraćanja pažnje na sledeće procese. Štaviše, pošto obična automatska mašina nema autodijagnostičku aparaturu, sitan nedostatak može proizvesti čitavu seriju defektnih delova. Autostop uređaji su ugrađeni u sve Toyota mašine da bi se tako nešto sprečilo.
Posetilac u Toyota fabrikama mora da zapazi velike signalne table koje vise sa tavanice. Kada se neka mašina zaustavi, pojavi se njen identifikacioni broj na signalnoj tabli. Operater tako zna kojoj mašini treba da posveti pažnju. TPS je osmišljen sa namerom da održi jednak protok proizvoda različitih jedinica čitave godine. Tako se izbegavaju zagušenja u bilo kom trenutku, kao što je kraj meseca. Izgleda da je ovaj sistem osposobljen da izađe na kraj sa zahtevima promeljivog tržišta, kojeg karakterišu sporiji rast i raznovrsna potražnja.
Očigledno je da je TPS zasnovan na kaizenu i TQC-u. U takvom sistemu bi mašine stalno stajale ako kvalitet ne bi bio održavan na visokom nivou u svim fazama proizvodnje, uključujući i podugovarače. Nije slučajno što su pet od osam dobitnika nagrade Japan Quality Control upravo kompanije iz Toyota grupe.
Toyota je postigla kaizen u oblastima kao što su layout fabrike, velikoserijska proizvodnja vs. stalna proizvodnja, česte izmene podešavanja i stav radnika. Drugim rečima, kamban i just in time koncepti predstavljaju rezultat napora za poboljšanjem u svim navedenim oblastima, napora koji su dostigli vrhunac u oblasti zaliha.
Napor kompanije Toyota za ostvarenjem kaizena u vitalnim oblastima je omogućio dostizanje 10 puta veće stope povraćaja kapitala od američkih proizvođača automobila. Zenzaburo Katayama, pomoćnik menadžera u promotivnom TQC odeljenju kompanije
Toyota Motors, kaže:
TPS u suštini omogućava da se traženi broj delova i komponenti proizvede i prosledi do montažne linije, tako da montaža ne prestane. To je sistem koji prolazi kroz svakodnevne promene i poboljšanja. Ponekad se TPS naziva i „sistem bez zaliha“. Treba reći da to nije tačno. Uvek imamo nešto zaliha pri ruci pošto nam je izvesni nivo zaliha neophodan za proizvodnju potrebnog broja proizvoda za određeno vreme...
Na prednjem delu karoserije svakog automobila na montažnoj liniji je kartica. Kola dobijaju različite delove i komponente, na osnovu brojeva i šifri na kartici. Moglo bi se reći da svaki automobil ima pričvršćen znak na kojem piše: „Hteo bih da postanem takav i takav automobil.“
Na primer, na kartici može biti zahtev za upravljač na levoj strani ili automatski menjač. Radnik na montažnoj traci uzima deo na koji upućuje uputstvo sa kartice. To se ponekad naziva Visual Management. Drugim rečima, radnik kontroliše proces posmatrajući karticu. Radnikovo znanje i ideje su uključeni u izgradnju boljeg proizvodnog sistema.
Na primer, kartice na prednjem delu karoserije automobila na montažnoj liniji su raznobojne da bi se izbegle greške. Ta ideja je potekla iz radničkih redova. Obučena i disciplinovana radna snaga je neophodna za funkcionisanje ovakvog sistema. Još jedna karakteristika sistema jeste ta što ćete izgubiti novac ako ga usvojite a nemate delove zadovoljavajućeg kvaliteta. Linija se zaustavlja kad god se uoči deo nezadovoljavajućeg kvaliteta.
U kompaniji Toyota zaustavljamo čitavu liniju kada opazimo defektni deo. Pošto su sve operacije u fabrici usklađene, efekat se prenosi do prethodnih procesa, sve dok i Kamigo fabrika koja proizvodi motore ne stane. Ako se zastoj produži, staće sve fabrike. Zaustavljanje fabrike je ozbiljan udarac menadžmentu. I pored toga, imamo hrabrosti da zaustavimo proizvodnju zato što verujemo u kontrolu kvaliteta. Kada smo već navukli nevolju na vrat i zaustavili fabriku, moramo pronaći uzrok problema i usvojiti kontramere, tako da se isti problem nikada ne ponovi.
Na primer, radnik u fabrici Tsutsumi može da pritisne dugme za zaustavljanje zato što je utvrdio da motori iz fabrike Kamigo nisu ispravni. Ne mora da zaustavi liniju, ali je ovlašćen da pritisne dugme za zaustavljanje kad god primeti bilo kakvu neusaglašenost. Kada se linija zaustavi, inženjeri i nadzornik će pohitati da vide šta nije u redu. Utvrdiće da su neispravni motori uzrok zaustavljanja. Ako se pokaže da su motori zbilja neispravni, inženjeri iz fabrike Kamigo će požuriti do Tsutsumi postrojenja da prouče problem. Sve fabrike će u međuvremenu prestati sa radom. Automobili neće izlaziti iz njih. Ipak, ma šta da se desi, moramo pronaći uzrok. Među odlikama japanske kontrole kvaliteta je izgradnja dobrih proizvodnih procesa.
Još jedna odlika TPS koncepta je način na koji prosleđuje i koristi informacije. Umesto da se u kontroli proizvodnje i raspoređivanju oslonimo na kompjutere, koristimo sredstva poput kambana i kartica pričvršćenih za karoseriju automobila u fabrici za montažu. Uobičajeno je da su proizvodi (delovi) i informacije razdvojeni u proizvodnji. Sa druge strane, svaki proizvod (deo) u kompaniji Toyota nosi svoju informaciju i signale. Od naših radnika očekujemo da koriste mozak i da čitaju i tumače informacije i signale na kamban karticama. Očekujemo da učestvuju u doterivanju sistema novim idejama.
U takvom sistemu, čak i kada radnik pogreši i montira pogrešan deo, problem ostaje na nivou jedinstvene greške koja ne stiže do naredne operacije. Kada skladištite voće i meso, stavljate ih u zamrzivače i frižidere da ne istrunu. I gvožđe truli na svoj način. Tehnološki razvoj izaziva promene u dizajnu. Komad gvožđa zastarelog dizajna je isto što i trulo voće, podjednako su neupotrebljivi.
Dodao bih da i informacije trule. Prikupljena a nepravilno uskladištena informacija brzo truli. Svaki menadžer koji ne prosleđuje informaciju zainteresovanim stranama i svaki menadžment bez sistema za upotrebu informacija čini veoma lošu uslugu kompaniji i stvara gomile škarta u obliku propuštenih prilika i protraćenog menadžerskog vremena.
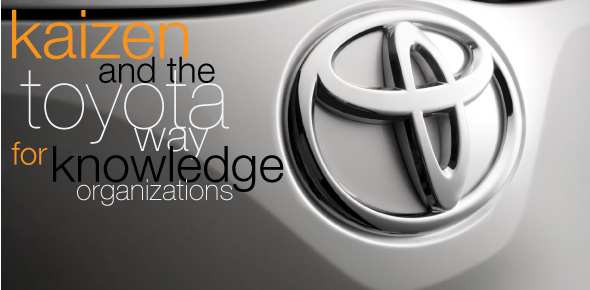
Mnogi menadžeri informacije smatraju izvorom autoriteta i pokušavaju da kontrolišu podređene stvarajući informativni monopol. To često rade rizikujući da žrtvuju organizacionu efikasnost. Menadžeri mogu biti potpuno nesvesni vrednosti informacije i doprinosa koji bi ona mogla dati ako bi stigla do pravih ljudi u pravo vreme. Čak i kada menadžer gaji iskreni interes za podelu informacija sa drugim direktorima, to zna biti otežano geografskim preprekama. Sa tim problemom se suočavaju brojne multinacionalne kompanije sa sedištem u Sjedinjenim Državama.
Na primer, kako podeliti važne informacije za razvoj novih proizvoda ako je sedište prodaje u Denveru, dizajnerski sektor u Masačusetsu, a fabrika u Šaumburgu? Ne radi se o problemu fizičke razdaljine. Psihološki otpor ljudi smeštenih na različitim lokacijama može biti znatna prepreka menadžmentu koji namerava da uvede kaizen u način prikupljanja, obrade i korišćenja informacija.
Ovaj tekst je preuzet iz knjige "Kaizen", Masaaki Imaija. Masaaki Imai je najveći svetski ekspert za implementaciju kaizena, kao i osnivač Kaizen Instituta koji posluje u preko 60 zemalja sveta, a od 2015.godine i u Srbiji. Knjigu možete naručiti preko ovog linka.