KO ČEKA, TAJ (NE) DOČEKA - Kaizen
Vaši zaposleni čekaju? Vi to sebi ne možete priuštiti.
Čekanje opisuje situacije kada se javlja stanje mirovanja koje prouzrokuju materijali, mašine, inspekcija ili informacije kada nisu u pravom trenutku spremni za ljude. Ovaj gubitak je najčešće manje uočljiv u odnosu na ostale zato što dolazi do česte zabune i mešanja sa prekomernom proizvodnjom. Kada čekanje postane uočljivo treba odvratiti zaposlene da proizvode više nego što je potrebno, samo da bi izgledali uposleno i taj rad donosi više štete nego koristi.
Postoje mnogi primeri čekanja. Najočigledniji je u slučaju kad operateri nisu u stanju da rade svoj posao jer čekaju isporuku materijala ili čekaju kontrolu da verifikuje izvršeni posao. Još jedan primer čekanja javlja se kada su radnici primorani da čekaju mašinu ili opremu kako bi postali dostupni bilo zbog lošeg planiranja ili neplaniranog zastoja. Takođe, često u fabrikama dolazi do čekanja usled koga radnici nisu u mogućnosti da obavljaju svoj posao zato što čekaju viljuškar da dođe. Čekanje može nastati pri čekanju informacija bez kojih nije moguće pristupiti izvršavanju operacija.
Čekaje je direktno povezano i prouzrokuje smanjenje kapaciteta, povećanje operativnih troškova i troškove prekovremenog rada. I pored činjenice da su svi zaposlenmi prisutni zbog čekanja koje se javlja neće biti moguće stvaranje željenog nivoa izlaza što nekad, usled ugovora sa korisnicima, dovodi do neophodnog prekovremenog rada.
Čekanje isto tako smanjuje sposobnost kompanije da bude fleksibilna kako bi mogla da isprati sve promene zahteva kupaca. Čekanje takođe vodi ka prekomernoj proizvodnji što na prvi pogled ne deluje logično. Zaposleni usled čekanja ne mogu izvršavati planirane operacije i javlja se sklonost ka proizvodnji proizvoda koja nije zahtevana od strane korisnika što stvara gubitke prekomerne proizvodnje.
Gubitke u čekanju možemo umanjiti/eliminisati primenom više različitih metoda i koncepata.
Početna metoda koja nam može pomoći pri fokusiranju na ovu vrstu gubitaka je uređenje proizvodne linije i Takt vremena. Ovaj metod takođe uključuju optimalni raspored u proizvodnoj liniji kako bi se osigurala balansiranost posla na takav način da ne postoji operator na čekanju. Potrebno je balansirati ciklusno vreme svakog procesa sa Takt vremenom.
Sledeće što možemo primeniti je jednokomadni tok (One piece flow). Ovaj koncept predstavlja tehniku koja obezbeđuje tok proizvoda u kome svaki operater radi samo na jednoj jedinici proizvoda i rad je iniciran potrebama narednog operatera. Uspostavljanjem jednokomadnog toka eliminiše se vreme čekanja, uzevši u obzir da je posao balansiran i tok u proizvodnji se odvija bez zastoja kroz konstantan proces.
Dobro definisani standardizovani dokumenti i vizuelni menadžment takođe predstavljaju veoma bitne metode koje targetiraju gubitke u čekanju. Svaki zaposleni kroz ove metode ima detaljno predstavljeno šta treba da radi, ali isto tako može da pomaže drugim zaposlenima u slučaju da na njegovoj poziciji ne postoji planirani posao ili je obim planiranog posla nedovoljan da popuni radno vreme.
Lean koncept Hejunka predstavlja nivelisanje proizvodnje i veoma je važan za čekanje. Bez ikakvog vida nivelisanja proizvodnje velike oscilacije u potražnji mogu dovesti do situacije da postoji previše posla koji se ne može postići, ili situacije kada postoji premalo posla tj. čekanje. Dakle, nivelisanjem proizvodnje kompanija je u mogućnosti da napravi plan proizvodnje i raspored nabavke resursa u smislu da ne dođe do čekanja ili preopterećivanja radne snage.
U slučaju da želite da proširite Vaše znanje o ovoj temi posetite sajt www.rs.kaizen.com gde možete videti primere uspešne primene Kaizen alata. U odeljku „Izdavaštvo“ postoji spisak knjiga u kojima je predstavljeno dugogodišnje iskustvo različitih autora iz oblasti Kaizena. Uskoro će u izadavaštvu Kaizen Instituta Srbija biti objavljeni prevodi knjiga „Kaizen: ključ japanskog konkurentskog uspeha“ i „Gemba Kaizen“ autora Masaaki Imai-a, najvećeg gurua i pionira Kaizena.
敬具
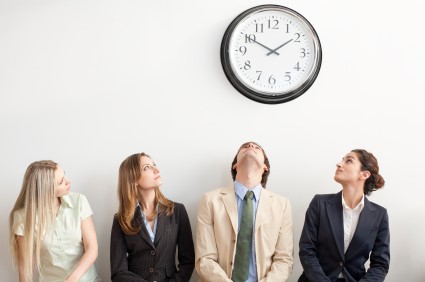
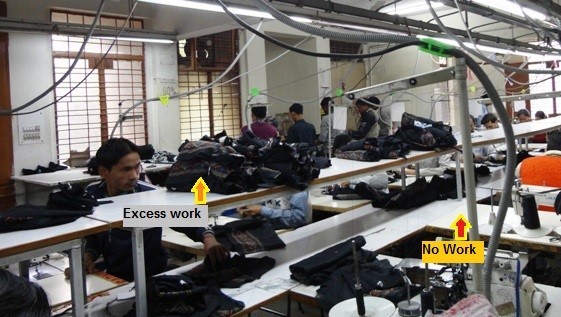