DA LI MOŽEMO ISTO ŠTO I JAPANCI? - Vladan Matović (Production Manager), Strauss Adriatic
U svakodnevnom životu ona uličica koju ste „provalili“, a koja vam štedi dva semafora i skraćuje put do kuće za celih deset minuta je Kaizen. Ono zavučeno parking mesto u tržnom centru koje većini promakne, jer su ponašanja ljudi predvidiva, je Kaizen. Kažem većini, jer niste samo vi analizirali putanje ljudi kroz garaže, niste samo vi radili statističku analizu koliko ste tu puta našli prazno mesto u odnosu na broj dolazaka, niste samo vi provodili sate tražeći parking i shvatili da vam malo razmišljanja i matematike može pomoći da uštedite vreme. Sve su to prirodne situacije koje je neko prepoznao kao gubitak i standardizovao u alate za analizu i eliminaciju. Ako je garaža Gemba, prostor u kome se odvija proces, ako ste vi primenili alate da dođete do poboljšanja, a ima ih preko dve stotine i ako vam je to postao novi standard - put ili parking mesto koje prvo „čekirate“, onda ste odradili ozbiljan Kaizen projekat! Uz uštedu vremena, imali ste još i manju emisiju gasova u atmosferu jer je motor kraće radio, smanjili ste broj radnih sati opreme, u ovom slučaju, auta, tako da je projekat uspeo - čestitam!
Uz rečenicu navedenu u naslovu, postoje još dve rečenice koje najčešće čujem kada me neko pita o Kaizenu, a to su: “Nismo mi Japanci” i “Naša industrija je baš specifična.“ Kada razmišljam o ove tri rečenice, sklon sam da se bar sa dve složim - sa tim da nismo mi Japanci, ili bar većina građana Srbije to nisu, i da je svaka industrija, pa i kompanija, specifična. Ono sa čim se ne mogu da se složim je da “to” (Kaizen) ne može kod nas. Jedan od razloga mog neslaganja je i taj što nema razloga da nešto što može bilo gde na svetu da se primeni, ne može da se primeni kod nas. Drugi razlog je što „to“ već radi kod nas.
Ako analiziramo samu reč Kaizen, gde kai znači – promena, a zen - na bolje, što bi u slobodnom prevodu značilo poboljšanje, dolazimo do zaključka da je svaka promena na bolje već Kaizen. Celokupna prethodna priča služi da razbije famu o nemogućnosti uvođenja metoda unapređenja (Kaizen) ili poboljšanja u bilo koji poslovni proces. Mi u kompaniji Strauss Adriatic se metodama unapređenja bavimo od 2009. godine kada smo prvi put videli praktične primene u raznim industrijama. Ono što je u tom trenutku bilo karakteristično je da je bilo vrlo malo domaćih firmi koje su to implementirale, dok je većina velikih multinacionalih kompanija sa tradicijom od pedeset ili više godina na tome bazirala svoj rad. Moje mišljenje je da za to postoje tri razloga:
Povećavaju se operativni troškovi
Analiza gubitaka troši resurse. Svakom poboljšanju prethodi detaljna analiza, odnosno, definisanje cilja, merenje operativnih vremena, razlaganje gubitaka, pronalaženje uzroka. Nakon toga sledi eliminacija uzroka gubitaka, provera da li je eliminacija gubitka trajna, formiranje novog standarda i sl. Sve to zahteva ljudske resurse, vreme, materijal, nekad i pomoć van organizacije. U knjigama se to vidi kao trošak. Ovde je jako važno da se napomene da ovi troškovi predstavljaju ulaganje u jednu od najvažnijih vrednosti kompanije a to su njeni zaposleni. Učestvovanjem u ovim projektima zaposleni jačaju povezanost sa kompanijom, šire svoja znanja i postaju još značajniji delovi procesa. Razvijanjem procesa, postavljanjem novih standarda i postupanjem po njima, zaposleni stabilizuju proces i na taj način pripremaju teren za naredna unapređenja. Kroz Kaizen projekte srednjeg i višeg nivoa sarađuju po horizontalnoj liniji sa kolegama iz drugih procesa, ruše percepciju koja još uvek postoji u kompanijama da je svaki proces silos za sebe i da je moguće funkcionisati nezavisno. Sa kolegama iz drugih procesa stvaraju sinergiju i omogućavaju da 2+2 ne bude 4, već 5 ili 6. Najveći napredak koji jedna kompanija može da ostvari je da zaposleni u različitim procesima deluju kao jedan tim. To je osnova na koju se nadograđuje „pull“ sistem tako da se u vrednosnom toku kompanije samo dodaju vrednosti, a gubici se zadržavaju u prethodnom procesu. Na taj način se eliminiše i prekomerna proizvodnja, brža je rotacija zaliha, Cash Flow je bolji, stvari se rade efikasnije, brže i nepotrebne akcije se eliminišu. Mi u Strauss-u implementiramo oko 60% predloga godišnje, evaluiramo rezultate predloga, nagrađujemo najbolje predloge, objavljujemo javno nagrade i nagrađene.
Posvećenost rukovodstva u ovom delu se ogleda u podršci da se ovi troškovi odobre zarad „višeg cilja“, podržavaju angažovanje zaposlenih, motivišu zaposlene i promovišu rezultate. Troškovi koji tom prilikom nastanu su minimalni spram benefita koji u perspektivi donose.
Ovaj tekst je preuzet iz Controlling magazina #10. Ceo magazin možete pročitati na ovom linku.
- Rezultati nisu odmah vidljivi
- Na budžetskom nivou se ne vide uštede
- Povećavaju se operativni troškovi
- 5S
- Visual Management
- Employee Suggestion System (ESS)
- One Point Lesson (OPL)
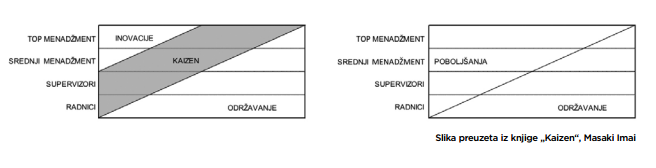
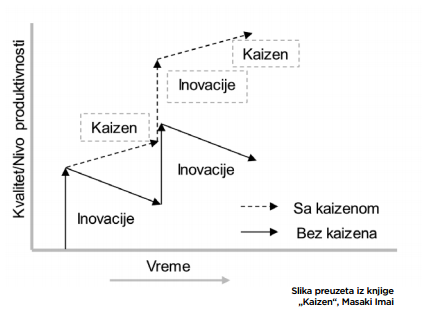