DA LI JE BOLJE POVUĆI ILI POTEGNUTI?- Milan Đorđević (Production Manager and Head of Machinning Department), Wacker Neuson
Moj prvi susret sa Lean konceptom, odnosno Kaizenom bio je na predavanju na Mašinskom fakultetu u Kragujevcu davne 2004. godine. U taj svet uveo nas je prof. dr. Nenad Mirić koji je tada radio u Kanadi kao iskusni inženjer u automobilskoj industriji. Profesor je prevalio dugačak put preko Atlantika da bi nama studentima, ali i direktorima većih firmi u Kragujevcu približio Kaizen - japansku filozofiju proizvodnje koja je tada već uzela maha i u Kanadskoj industriji.
Predavanje je bilo veoma interesantno i slikovito, a prikazane su skoro sve tehnike Leana, kao i prednosti 5S, VSM, JIT, Kanbana, TPM (Total Productive Maintenance), i mnogo toga još…Na to predavanje sada gledam kao na pokušaj grupe ljudi, odnosno čoveka koji je uspeo u svetu, da pokaže mogući put za izlazak iz tako teške situacije u kojoj se privreda grada nalazila.
Naravno, kod nas je kriza bila u punom jeku, nezaposlenost velika, firme tonu sve dublje i dublje u gubitke. Generalno govoreći, naši proizvodi su bili preskupi jer su troškovi proizvodnje bili visoki, a profesor je govorio o tehnikama koje bi pomogle da se troškovi smanje ili eliminišu. Govorio je o Lean konceptu.
Međutim,iznenadilo me je nerazumevanje i otpor prisutnih slušalaca, mi studenti bili smo pomalo zbunjeni i sve mi je to izgledalo tako daleko pa sam zaključio: Ovo se kod nas nikada neće dogoditi.
Prošlo je nekoliko godina nakon tog predavanja, ja sam završio fakultet, počeo da radim u manjoj firmi i od svega mi je tada ostalo mutno sećanje na jednu lepu priču koja postoji negde daleko u zemlji snova.
U međuvremenu prilike su kod nas pocele da se blago popravljaju i 2010. godine počinjem da radim u nemačko-austrijskom koncernu Wacker Neuson. Mlada, internacionalna, dinamična kompanija sa jakim akcentom na rast i razvoj, firma u kakvoj sam oduvek želeo da radim! Počeo sam kao inženjer u proizvodnji poluproizvoda za građevinske mašine. Nije prošlo ni nekoliko meseci od početka rada, a u firmi je krenuo pilot–projekat implementacije Kanban sistema na jednoj od proizvodnih linija. Projekat su vodili konsultanti iz Austrije. Obučavali su nas i pokazivali isto ono što sam slušao od profesora Mirića šest godina ranije!
Push vs. pull
Prve aktivnosti bile su usmerene na implementaciju pull sistema umesto dotadašnjeg push sistema. Razlika je u upravljanju proizvodnjom:
U push varijanti imali smo proizvodnju i izdavanje radnih naloga na osnovu nedeljnog i mesečnog plana koji smo pratili u Excel tabeli. Tu su bile definisane i potrebne količine. Moj glavni zadatak tada bio je tada svakodnevno štampanje radnih naloga za proizvodnju i 90 odsto svog vremena trošio sam na tu aktivnost. Na kraju dana radio sam zatvaranje realizovanih radnih naloga kroz SAP - ogroman administrativni posao! Skoro svakodnevna pojava bila je promena plana proizvodnje, uzrokovana potrebama kupaca. U tako dinamičnom okruženju dolazilo je do propuštenih naloga, ili do kašnjenja u njihovom izdavanju. Nepredvidljvost situacije uzrokovala je prekomernu proizvodnju artikala, po sistemu just in case („za svaki slučaj”), što je za posledicu imalo povećanje potrošnje sirovina i pomoćnog potrošnog materijala. Takav nepredvidiv sistem odrazio se i na naručivanje sirovog materijala u smislu njegovog bespotrebnog nagomilavanja. Upotreba resursa i kapaciteta mašina i radne snage nije odgovarala potrebama kupaca u datom trenutku, jer često se dešavalo da nekih artikala imamo previše na stanju, dok drugi nedostaju! Znači, celokupan sistem bio je inertan, spor da odgovori izazovima proizvodnje. Sve ovo imalo je, naravno, i finansijsku pozadinu, što se jasno moglo videti u pracenju KPI.
Promena je nastala u toku 2012. uvođenjem Kanban supermarketa koji se nalazio između linije za proizvodnju poluproizvoda i linije za izradu gotovih proizvoda. Svaki artikal dobio je karticu na kojoj je bila odštampana nedeljna prosečna količina, jedinstven SAP broj, postupak izrade i adresa na polici. Znači, radni nalog u malom. Uz to, kartica je imala i bar-kod na sebi, pa se otvaranje i zatvaranje naloga/kartice vršilo skeniranjem. Artikli su bili spakovani u dve identične metalne kutije (bin1 i bin2), označene SAP brojem i u svakoj se nalazila dvonedeljna količina. Time smo ograničili zaihe, kao i veličinu serije odnosno lot-a. Kada bi se na proizvodnoj liniji koja je imala ulogu internog kupca, ispraznio prvi bin, bio bi poslat na liniju poluproizvoda zajedno sa karticom i to je bio automatski signal za početak proizvodnje.Pre toga, imali smo magacin poluproizvoda koji je dosezao skoro do krova hale i koji je zauzimao ogroman prostor, zahtevao dodatnu logistiku i opsluživanje.
Rezultat i finansijski efekti
Iako je bilo straha, sumnje i otpora prema ovako drastičnoj promeni, prvi rezultati bili su vidljivi u brzini kojom se obavljao posao. Nije bilo gubitaka u komunikaciji kao ranije, a uz FIFO sistem (First In First Out) jasno smo definisali prioritete. Prazan bin koji bi stigao prvi na liniju, prvi je i uziman za izradu. Ostale uštede bile su ogromne.
Količina materijala WIP-u (Work In Progress) osetno se smanjila, uz porast koeficijenta godišnjeg obrta. Takođe, zalihe sirovog materijala opale su za oko 30 odsto, a magacin gotovih proizvoda je bio u stalnom porastu. Vrednost magacina pomoćnog potrošnog materijala opala je za 20 odsto. Ono što se jasno videlo kao pozitivna promena KPI je period zadržavanja zaliha u danima.
Takvi pozitivni pokazatelji odagnali su sve sumnje kojim putem treba ići u proizvodnji i Wacker Neuson je snažnim koracima nastavio da se razvija u pravcu pull sistema.
Za mene lično to je bilo veliko iskustvo koje mi je donelo osećaj zadovoljstva što sam bio deo uspešne priče koja je do juče bila moguća samo „tamo negde daleko na Zapadu”. Osećao sam ponos i sreću što učestvujem u svemu tome i što je moja firma rešila da krene tim putem. Znači, ipak se kreće!
Ovaj tekst je preuzet iz Controlling magazina #10. Ceo magazin možete pročitati na ovom linku.
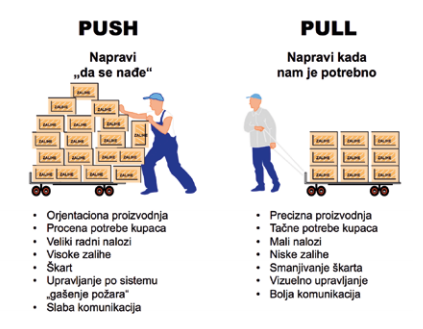
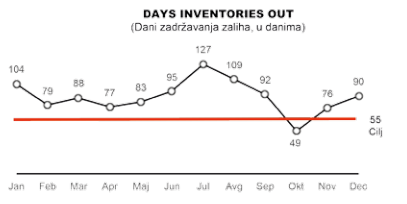