KADA JE 1% MNOGO? - Kaizen
Treba težiti konceptu Zero Defects! Kvalitet se dugo pamti i kad se cena zaboravi.
Svaki rad koji ne isunjava zahteve korisnika se definiše kao defekt. Defekti predstavljaju veoma veliki problem za svaku kompaniju. Veoma je teško kvantifikovati troškove lošeg kvaliteta, ali se njihov uticaj najčešće posmatra kroz troškove garancije, smanjen kapacitet poizvodnje, troškove dorade, troškove popravki na terenu, ali najbitnije od svega kroz gubitak korisnika.
Postavlja se pitanje koji je nivo škarta dozvoljen, odnosno, koliko treba proizvesti dobrih proizvoda koji zadovoljavaju zahteve korisnika. Da li je 99% dovoljno? Koliki uticaj ima 1% defekata na poslovanje posmatraćemo kroz rezultate studije Gemba Academy-je sprovedene u Americi:
Alati koji se koriste kako bi se smanjio nivo defekata:
U slučaju da želite da proširite Vaše znanje o ovoj temi posetite sajt www.rs.kaizen.com gde možete videti primere uspešne primene Kaizen alata. U odeljku „Izdavaštvo“ postoji spisak knjiga u kojima je predstavljeno dugogodišnje iskustvo različitih autora iz oblasti Kaizena. Uskoro će u izadavaštvu Kaizen Instituta Srbija biti objavljeni prevodi knjiga „Kaizen: ključ japanskog konkurentskog uspeha“ i „Gemba Kaizen“ autora Masaaki Imai-a, najvećeg gurua i pionira Kaizena.
敬具
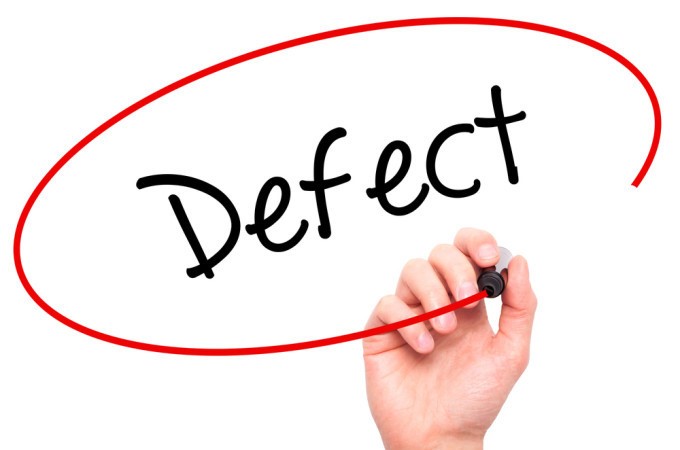
- Ako bi sve apoteke u radile sa 1% defekata, na godišnjem nivou bi izdavale 20.000 pogrešnih recepata,
- Ako bi aerodrom Dallas Fort Worth radio sa 1% defekata, na dnevnom nivou bi imao 2 prekratka ili preduga sletanja,
- Ako bi pošte radile sa 1% defekata bilo bi oko 400 izgubljenih pošiljki po satu.
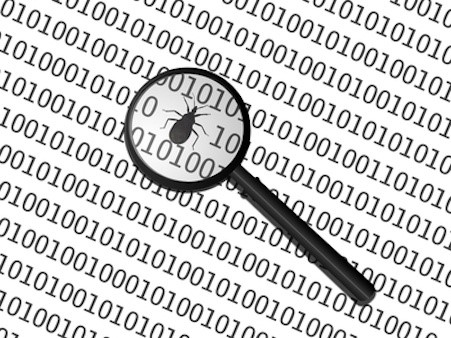
- Princip zaustavljanja proizvodne linije koji ohrabruje i obavezuje svakog zaposlenog da zaustavi proizvodnu liniju ako uoči neusaglašenost na proizvodu. Veoma važan segment ovog principa je razumevanje nastanka defekta i otkrivanje uzroka. Mnoge kompanije koje su upoznate sa principima Lean proizvodnje koriste Andon kao alat za zustavljanje proizvodne trake. Jednostavnim povlačenjem kabla aktivira se Andon sistem koji momentalno zaustavlja proizvodnu traku i svetlosnim signalima upućuje na mesto gde je detektovana neusaglašenost,
- Jedan od veoma moćnih alata je Poka Yoke koji predstavlja alat za prevenciju grešaka. Ovim alatom se vrši inteligentno poboljšanje samog sredstva za rad ili procesa kako bi se eliminisala verovatnoća pojave greške,
- Pri identifikaciji problema neophodno je utvrditi i sam uzrok problema. Metode koje koristimo za definisanje korena uzroka problema su 5WHY i 4M,
- Jidoka predstavlja sistem automatizacije za ljudskim dodirom. Sistem je osposobljen na samostalno detektuje neusaglašenost i svetlosnim signalima poput Andona naznači gde je detektovan defekt. Nakon toga sledi identifikovanje uzroka problema i korektivna akcija što predstavlja ljudski dodir iz definicije sistema. Ovaj sistem važi za jedan koji iziskuje određena finansijska ulaganja ali to nije uvek slučaj. Nekad je dovoljno motiranje senzora na komandni registar mašine kako bi se sistem uspostavio,
- Primena Six Sigma metodologije je statistički pristup koji organizacija može da primeni u borbi sa defektima. Ova metodologija se zasniva na proizvodnji 3.4 defektna proizvoda na milion proizvedenih,
- Veoma bitan princip je i obezbeđivanje jasne radne dokumentacije i procedura svim zaposlenima kako bi se uvećala verovatnoća da se proizvede proizvod koji ispunjava sve propisane zahteve.
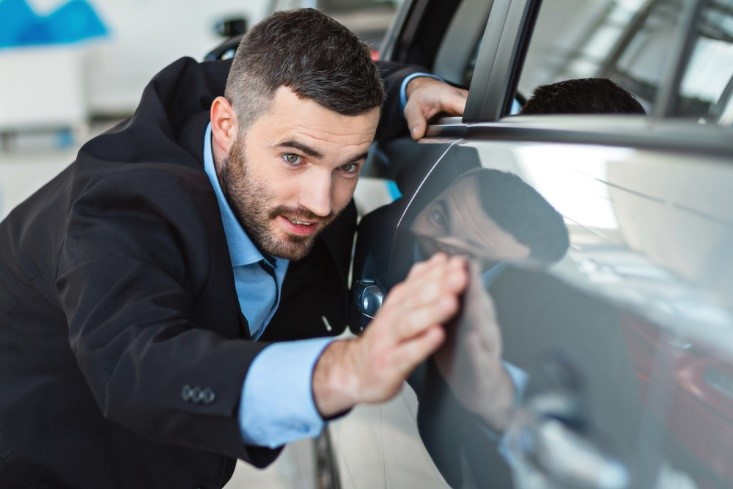