"MRŠAVA" PROIZVODNJA = "MRŠAVO" SNABDEVANJE - Milan Milenković (Gemba Kaizen Lider), Johnson Electric
Najčešći izgovori pri ideji o uvođenju Kanbana su: to ne može da funkcioniše kod nas zbog naših dobavljača; mi smo specifični... ili, postavljanje pitanja šta će se desiti ako neka komponenta nestane u toku proizvodnje. Ključno kod implementacije je da ne razmišljate o potencijalnim problemima, već da aktivno tražite rešenja. Uvođenje Kanban načina planiranja proizvodnje zahteva preokret u dosadašnjoj praksi poslovanja fabrika. Treba promeniti način razmišljanja zaposlenih kako bi razumeli da gomilanje materijala ili poluproizvoda znači bacanje novca
Kao deo Lean proizvodnje, važna oblast je planiranje materijala. Lean ili „mršava“ proizvodnja podrazumeva i „mršavo“ snabdevanje zalihama jer je suština postići manji trošak, zarobiti što manje kapitala i ostati konkurentan na tržištu. Termin pull flow ili, Kanban planiranje proizvodnje, označava povlačenje materijala sa uzvodnih procesa shodno potrebnoj količini. Ako bi hteli da pojednostavimo - nabavljamo materijala onoliko koliko možemo da prodamo gotovih proizvoda.
Postoje preduslovi za nesmetano uvođenje Kanbana u proizvodnji. To su: smanjiti obim po jednoj isporuci repromaterijala, odnosno povećati frekvenciju dovoženja materijala; mapirati sva uska grla u procesima proizvodnje i investirati svoje vreme i vreme zaposlenih u samoj implementaciji. Treći uslov, iako zvuči najmanje bolno, ujedno zahteva i najveće angažovanje. On podrazumeva dodatan napor zaposlenih u definisanju veličina proizvodnih šarži, kreativnost u jednostavnim i ergonomskim rešenjima transportnih sredstava unutrašnje logistike, kao i motivaciju zaposlenih zarad održavanja i poštovanja uspostavljenog sistema nakon implementacije.
Kao i u svakom poslu, ili izboru u kom se nađemo u životu, i ovaj sistem ima svoje prednosti i mane. Na nama je da sve prednosti kao takve odmah iskoristimo, a mane pretvorimo u šanse.
Prednost Kanban planiranja jeste što je vrlo jednostavan. Dakle, svi zaposleni u kompaniji vrlo brzo mogu da ga nauče i primene. Možda vam neće biti potrebni skupi ERP programi, njihovo implementiranje koje traje mesecima, preskupe obuke, vreme konsultanata i sva ona prateća oprema koja ide uz njih. Takođe, neće vam biti potrebna glomazna odeljenja planiranja materijala, kreiranja dnevnih, nedeljnih i mesečnih planova proizvodnje, komplikovane Excel tabele koje prate zahteve kupaca, kapacitet linija, utrošak materijala... Kanban ne ukida zaposlene u odeljenju planiranja, ali pravi znatne uštede i komfor u odeljenju i pomaže zaposlenima.
Druga prednost je vizuelna kontrola zaliha. Jednim pogledom na supermarket vi imate uvid u količine zaliha. Dobijate odmah odgovor na pitanja - da li je materijal u supermarketu u granicama planiranog, da li su svi Kanbani popunjeni u skladu sa definisanom količinom ili je supermarket pretrpan repromaterijalom koji stoji nekoliko nedelja i možda postaje neupotrebljiv (korozija, istekao rok važenja...). U ovom slučaju nisu potrebni dodatni resursi za analizu zaliha, nije vam potreban zaposleni koji radi redovan ili vanredan popis, pretražuje fakture ili jednostavno radi posao za koji nas kupac ne plaća. Dovoljno je baciti pogled na policu, prebrojati palete i videti trenutno stanje zaliha tj. vašeg zarobljenog novca.
Treća prednost što Kanban sprečava prekomernu proizvodnju. Šta to konkretno znači za jednu fabriku? Ljudi u fabrici vole da igraju na „sigurnu kartu“, tj.sigurnija je proizvodnja ako napravimo malo više, da „se nađe“. Potrebno je onda temeljno sagledati sve izazove u procesima i osigurati da zalihe budu onolike koliko su zaista potrebne, ali ih ne određivati paušalno. Svaki višak zaliha košta i to je osnovni razlog uvođenja Kanbana.
Kako proračunati Kanban? Veličina šarže zavisi od vremena potebnog za zamenu proizvoda ili alata. Ako je ovo vreme predugo, to direktno povećava i veličinu šarže koja mora da pokrije taj interval dok mašina stoji. Samo aktivnostima na smanjenju trajanja ove aktivnosti mi možemo da utičemo i na veličinu zaliha, odnosno Kanbana. Obično se koristi formula:
Jedan primer: ako je vreme trajanja zamene alata 20 minuta, onda je veličina našeg Kanbana 20 minuta : 10% = 200 minuta. Sada tu informaciju treba pretvoriti u količinu proizvoda, dakle 200 minuta proizvodnje delimo sa taktom proizvodnje naše linije (npr. 10 sec) i dobijamo veličinu našeg Kanbana od 1.200 komada. Ovako dobijena veličina je minimalni broj proizvoda za koji se isplati menjanje alata jer, u protivnom, ako radimo različite reference u manjim veličinama od izračunate, onda ulazimo u zonu gde operateri više vremena provode u aktivnostima menjanja alata nego u proizvodnji.
Da bismo osigurali da naš supermarket u svakom trenutku ima spremne komponente za sledeći proces, moramo imati dve šarže, odnosno dva Kanbana - jedan koji se troši, tj. povlači nizvodno i jedan koji se proizvodi tj. dopunjuje supermarket. Ovakvom postavkom garantujemo da uvek imamo spremne zalihe za povlačenje, uvek imamo zalihe koje se kreću u opsegu minimalne i maksimalne zadate veličine, odnosno da imamo kontrolu troškova u svakom trenutku i osiguravamo kontinualno planiranje proizvodnje nizvodnih ciklusa povlačenjem zaliha iz supermarketa.
Kako funkcioniše planiranje nizvodnih procesa? Povlačenjem zaliha koji ulaze u jedan Kanban mi skidamo karticu koja stoji na punoj ambalaži i postavljamo je u red za proizvodnju. Ta kartica je informacija proizvodnji da je količina iz supermarketa iskorišćena i potrebna je dopuna zaliha. Kartica mora da ima sve potrebne informacije koje trebaju operateru da bi proizveo i spakovao traženi proizvod. Potrebne informacije su: broj komponente, opis, slika komponente, materijal, količina koja se pakuje, broj ambalaža i slično. Jednim pogledom na karticu svima bi trebalo da bude jasno šta proizvode, od čega i koliko. Na sledećoj slici je opisano kruženje Kanban kartica i informacija.
Ređanjem kartica različitih referenci mi pravimo redosled, odnosno plan proizvodnje. Uzmimo, na primer, da je u prvom satu linija montaže iskoristila dva proizvoda B, a u sledećem satu tri proizvoda A. To znači da bi pogled na naš redosled proizvodnje bio sledeći, dve kartice komponente B, iza njih tri kartice komponente A, i tako redom. Pogledom na taj red operater ima jasnu sliku šta proizvodi i u kojoj količini. Nakon proizvodnje odnosno dopune komponenti iste kartice se vraćaju na ambalažu i ostaju u supermarketu do narednog povlačenja materijala.
Iz ovog primera može se videti direktna ušteda u resursima i aktivnostima planiranja. U ovom slučaju ne treba nam osoba koja će u svakoj smeni popisivati zalihe, zatim to stanje unositi u sistem, pa iz tih sistema upoređivanjem sa potražnjom kupaca raditi plan proizvodnje za naredni dan. Sve je automatizovano jednostavnim karticama, a investicija je minimalna. Zahteva samo jednom premeravanje i preračunavanje veličina Kanbana i izradu jednostavnih kartica koje svako može da tumači bez dodatnih i komplikovanih instrukcija.
Ovako opisan proces planiranja je najlakše primeniti na high runner proizvodima, odnosno proizvodima koje neprekidno proizvodimo. Sa druge strane, postoji problem sa low runner proizvodima, odnosno proizvodima koje proizvodimo jednom nedeljno ili mesečno. Kod njih je isti princip, samo je potrebno malo više truda. Za ovakve proizvode možemo urediti planiranje na nekoliko načina. Jedan od načina je da definišemo veću količinu i pomirimo se sa tim da proizvodimo unapred, tj. zadržavamo više resursa nego što je potrebno. Time planiranje funkcioniše nesmetano za sve tipove proizvoda ali se protivi principima Lean proizvodnje. Drugi od načina je koristiti tzv. egzotične ili specijalne Kanban kartice na kojima je napisana tačna količina proizvoda koja treba biti proizvedena tog dana ili nedelje. Takve kartice je potrebno posebno planirati. Na primer, planer proizvodnje dobije informaciju da mu je potrebno 100 komada proizvoda u toku prve nedelje u toku meseca, a sledeća potreba je tek poslednje nedelje tekućeg meseca. Planer donosi karticu sa ispisanih 100 komada potrebnog proizvoda i stavlja je u red za planiranje proizvodnje. Kada dođe na red low runner se proizvodi i ostavlja u supermarketu. Nakon upotrebe tj. povlačenja poluproizvoda iz supermarketa, planer uzima karticu i vraća je tek poslednje nedelje meseca, kada je ponovo potrebna proizvodnja specifičnog materijala. Opisane aktivnosti troše više resursa, bilo da je u pitanju materijal, ambalaža, prostor u hali ili dodatno vreme planerima proizvodnje i zbog toga menadžment mora da uvidi šta je manje bolno za proizvodnju i da izabere adekvatan metod planiranja low runnera.
Kod planiranja proizvoda treba da uzmemo u obzir i uslove bezbednosti, praćenje sledljivosti upotrebljenog materijala i slično. Izazov sa kojim sam se sreo pri planiranju Kanbana na blanking procesu u preseraju je da i pored popunjavanja Kanbana prema definisanim karticama, proizvodnja mora da se nastavi zbog kompletiranja čeličnog kotura koji se iz bezbednosnih razloga kada je jednom postavljen ne skida sa odmotavača kotura. Na primer, od jednog čeličnog kotura moguće je proizvesti 10.000 nekih od presaka, a definisana količina po Kanbanu je 8.500 jedinica. Nakon popunjavanja Kanbana proizvodnja ima višak od 1.500 jedinica koje se ne mogu smestiti u supermarketu. Još kada se uzme u obzir da svaki čelični kotur ima različitu težinu, tj. broj jedinica koje mogu da se proizvedu, dobijamo ozbiljan izazov - kako precizno isplanirati i održavati pravila koja diktira Pull sistem? Jedno od rešenja je uvođenje tzv. „Banke proizvoda“. Sav višak jedinica koji je proizveden preko punog Kanbana pakuje se u standardnu ambalažu i postavlja u poseban deo supermarketa koji nazivamo „Banka“. On se povlači pri sledećem zahtevu za proizvodnjom tih jedinica. U tom slučaju planer ili operater ima specifičan zadatak da nakon prikupljanja Kanban kartica prvo povuče sav materijal iz „Banke proizvoda“ i Kanbane dopuni novim proizvedenim jedinicama. Ovakaj način omogućuje: održanje sledljivosti proizvodnje, FIFO i povećava bezbednost zaposlenih.
I u ovom slučaju potrebno je poštovati pravila, a to je da se broj kartica i redosledi moraju stalno proveravati. Ako neko odluči da umesto tri kartice proizvoda A, proizvede samo jednu ili dve, rizikuje da u nekom trenutku supermarket ostane nedopunjen i da više vremena provedemo u menjanju alata. Na početku implementacije ovo moramo kontrolisati dnevno, smenski i stalno ponavljati pravila zaposlenim. Ukoliko ne objasnimo značenje tih kartica ljudima koji direktno učestvuju u proizvodnji, onda je i manja šansa da oni poštuju pravila koja smo postavili. Ponavljanje stvara naviku, navika običaj, a običaj kulturu, a to je ono čemu težimo u našim organizacijama – visoko-obučenom osoblju koje živi kulturu organizacije i posvećeno je zajedničkim ciljevima. Promena kulture je i najteža stvar u celom ciklusu implementacije Pull sistema.
Kako ovo prevazići? Jedan od načina koji je primenljiv u praksi je omogućiti zaposlenima (operaterima, tehničarima) da aktivno učestvuju u definisanju i implementiranju Kanbana. Po mom iskustvu zaposleni posvećuju više pažnje ukoliko su sami kreirali kartice, ambalažu, kolica ili davali predloge pri implementaciji. Tako ne stiču utisak da je to još jedan besmisleni zadatak menadžmenta koji samo oni moraju da obavljaju. Inicijative od strane samih korisnika Kanban planiranja, tj. operatera, treba ohrabrivati pomoću kartica sugestija i ideja.
Da bi postigli zajednički cilj tj. usadili kulturu ponašanja koja bi zaposlenima olakšala svakodnevni rad, treba stalno edukovati ljude i praktično ih voditi kroz primere ne bi li uvideli kako se stvari vrlo brzo menjaju na bolje i da svaki problem ima rešenje ukoliko se timski radi na njegovom rešavanju. Implementacija Pull sistema ne traje jedan dan ili jednu nedelju. Poput Lean proizvodnje, potrebno je usmeriti sve zaposlene ka istom cilju, a to je maratonski posao, i tu činjenicu menažment mora da prihvati pre odluke o implementaciji. Takođe, implementacija se ne završava jednim štampanjem kartica i postavljanjem sekvencera, već je potrebno neprekidno nadgledati protok, uska grla, nagomilavanja materijala i stalno optimizovati procese. Jedna od ključnih stvari u Pull sistemu je SMED (brzina zamene alata) i koliko budemo uspešni u SMED-u, toliko ćemo biti uspešni i u Pull planiranju.
Tekst je preuzet iz Controlling magazina #10. Ceo magazin možete pročitati na ovom linku.

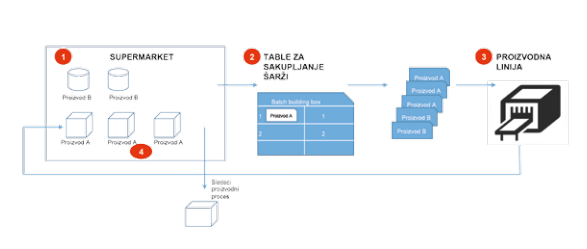